Clean room testing methods and procedures
22-01-18 17:28
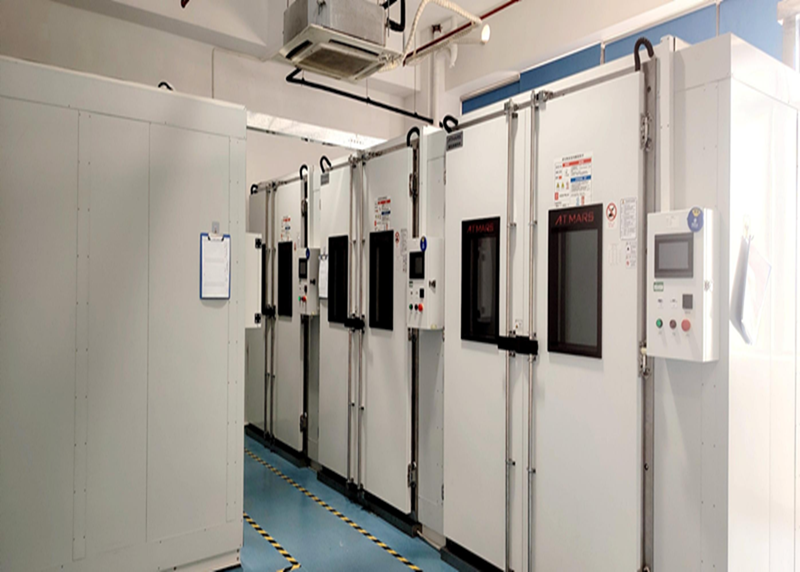
1. Concepts related to clean room
The clean area is a limited space where the concentration of suspended particles in the air is controlled. The construction and use should reduce the induction, generation and retention of particles in the space, and other relevant parameters in the space, such as temperature, humidity, pressure, etc., should be controlled.
Air cleanliness refers to the degree of the amount of dust particles in the air in a clean environment. The higher the dust concentration, the lower the cleanliness. The lower the dust concentration, the higher the cleanliness.
The specific level of air cleanliness is distinguished by the level of air cleanliness, and this level is expressed by the counted dust concentration of the air within the operating time.
Suspended particles refer to solid and liquid particles in the air suspended particle size range of 0.15μm for air cleanliness classification.
Two. Classification of clean rooms
1. According to the cleanliness level, it is divided into grade 1, grade 2, grade 3, grade 4, grade 5, grade 6, grade 7, grade 8 and grade 9. Level 9 is the lowest level.
2. According to the classification of air flow organization, the clean room can be divided into three categories: unidirectional flow, laminar flow, and clean room.
Airflow with parallel streamlines in a single direction and with uniform velocity across the cross section. One-way flow perpendicular to the horizontal plane is vertical one-way flow and one-way flow parallel to the horizontal plane is horizontal one-way flow.
Turbulent flow non-unidirectional flow clean room A clean room with an airflow that does not meet the definition of unidirectional flow. Mixed flow clean room: A clean room with a combination of unidirectional flow and non-unidirectional flow.
3. According to the classification of suspended particles in the air that need to be controlled, the clean room can be divided into industrial clean room and biological clean room.
Industrial clean room, its main control parameters are temperature, humidity, wind speed, air flow organization, and cleanliness.
The difference between the biological clean room and the industrial clean room is that the concentration of bacteria in the control room is added to the control parameters.
4. The detection status of the clean room can be divided into three categories.
(1) Empty clean room with complete facilities, all pipelines are connected and running, but there are no production equipment, materials and production personnel.
(2) Static The production equipment has been installed in a clean room with complete facilities and has been tested and transferred according to the method agreed by the owner and the supplier, but there are no production personnel on site.
(3) The dynamic facility is in the state of operating in the prescribed manner and the prescribed personnel are present to work in the prescribed manner.
3. The difference between clean air conditioner and general air conditioner
The difference between clean room and general ventilation and air conditioning system The clean room air conditioner is a kind of air conditioning project. It not only has certain requirements on the temperature, humidity and wind speed of the indoor air, but also has certain requirements on the number of dust particles and bacterial concentration in the air. etc. have higher requirements.
Therefore, it not only has special requirements for the design and construction of ventilation projects, but also has special requirements and corresponding technical measures for the design and construction of building layout, material selection, construction procedures, construction practices, plumbing, electricity and technology itself. also increased accordingly.
1. Main parameter control
General air conditioners focus on the supply of temperature, humidity, and fresh air volume, while clean room air conditioners focus on controlling the dust content, wind speed, and ventilation times of indoor air. In rooms where temperature and humidity are required, they are also the main control parameters. The bacterial content of the biological clean room is also one of the main control parameters.
2. Air filtration means
Some general air conditioners only have coarse-efficiency first-stage filtration, and those with higher requirements are coarse-efficiency and medium-efficiency second-stage filtration.
Clean air conditioners require three-stage filtration, that is, coarse, medium, and high-efficiency three-stage filtration or coarse, medium, and sub-high-efficiency three-stage filtration. In addition to the three-stage filtration in the air supply system of the biological clean room, in order to eliminate the special odor of animals and avoid pollution to the environment in the exhaust air system, a secondary high-efficiency filter or a poison adsorption filter is provided according to different situations.
3. Indoor pressure requirements General air conditioners have no special requirements for indoor pressure, but clean air conditioners have different requirements for positive pressure values in different clean areas in order to avoid the infiltration of external polluted air or the interaction of different substances in different production workshops. There are still negative pressure control requirements in the negative pressure clean room.
4. The selection of clean air-conditioning system materials and equipment, processing technology, processing and installation environment, and storage environment of equipment components all have special requirements in order to avoid external pollution. This is also not available in general air conditioning systems.
5. Requirements for airtightness
General air-conditioning systems have requirements for the air-tightness of the system.
However, the requirements for clean air-conditioning systems are much higher than those of general air-conditioning systems, and the testing methods are strict measures and testing requirements for the standards of each process.
6. Requirements for civil engineering and other types of work.
Generally, air-conditioned rooms have requirements for architectural layout and thermal engineering, but they do not pay much attention to material selection and air tightness.
The evaluation of building quality by clean air conditioners focuses on dust prevention, dust prevention, and leakage prevention in addition to the general building appearance requirements.
The construction process arrangement and lap joints are very strict to avoid leakage caused by cracks caused by rework.
Its cooperation and requirements for other types of work are also very strict, mainly focusing on preventing leakage to prevent external polluted air from penetrating into the clean room and preventing dust from polluting the clean room.
Four. Completion acceptance of clean room
After the clean room is completed and put into production, performance measurement and acceptance are required; when the system is overhauled or updated, a comprehensive measurement is also required, and the general situation of the clean room must be fully understood before the measurement.
The main content includes the plan, section and system diagram of the purified air-conditioning system and process layout, requirements for air environmental conditions, cleanliness, level, temperature, humidity, wind speed, etc., air treatment scheme, return air, exhaust air volume, and air flow organization. Purification scheme Clean room usage, factory area and its surrounding pollution, etc.
(1) The visual inspection of the clean room completion acceptance should meet the following requirements
1. The installation of various pipelines, automatic fire extinguishing devices and purification air-conditioning equipment air conditioners, fans, purification air-conditioning units, high-efficiency air filters and air shower rooms should be correct, firm and tight, and the deviation should comply with relevant regulations.
2. The connection between the high and medium efficiency air filter and the support frame and the connection between the air duct and the equipment should be reliably sealed.
3. All kinds of adjustment devices should be tight, flexible and easy to operate.
4. Purify the air conditioning box, static pressure box, air duct system and air supply and return air outlets without dust.
5. The inner wall, ceiling surface and ground of the clean room should be smooth, flat, uniform in color, free of dust, and free of static electricity on the floor.
6 The sealing treatment of the air supply and return air outlets and various terminal devices, various pipelines, lighting and power line piping, and process equipment passing through the clean room should be tight and reliable.
7. All kinds of switchboards and cabinets in the clean room and the electrical pipelines and nozzles entering the clean room should be sealed and reliable. 8 All kinds of brushing and heat preservation work should comply with relevant regulations.
(2) Commissioning of clean room manufacturing completion acceptance
1. The stand-alone trial operation of any equipment that requires trial operation shall comply with the relevant provisions of the equipment technical documents.
The general requirements belonging to mechanical equipment should also comply with relevant national regulations and relevant industry standards for the construction and installation of mechanical equipment. Usually, the equipment that needs to be tested by a single unit in the clean room includes air conditioning units, air supply pressurized fan boxes, exhaust equipment, purification workbenches, electrostatic self-cleaning devices, clean drying boxes, clean lockers and other partial purification equipment, as well as air shower rooms. , residual pressure valve, vacuum cleaning equipment, etc.
2. After the stand-alone test operation is qualified, it is necessary to set and adjust the air volume and air pressure adjustment devices of the air supply system, return air system, and exhaust system so that the air volume distribution of each system meets the design requirements.
The purpose of testing at this stage is mainly to serve the adjustment and balance of the air conditioning purification system, which often needs to be repeated many times.
This inspection is mainly carried out by the contractor, and the maintenance and management personnel of the construction party should follow up to familiarize themselves with the system.
On this basis, the joint test run of the system including cold and heat sources is generally not less than 8 hours. It is required that all equipment components in the system, including the purification air-conditioning system, automatic adjustment device, etc., should operate correctly and have no abnormal phenomena during the linkage operation and coordination process.
Five. Clean room testing process
All instruments and equipment used in the determination must be identified, calibrated or calibrated according to regulations. Before the measurement, the system, clean room, machine room, etc. must be fully cleaned; after cleaning and system adjustment, it must be continuously operated for a period of time and then the measurement of leak detection and other items must be carried out.
(1) The procedure of clean room measurement is roughly as follows:
1. Air blowing by fan
2. Indoor cleaning
3. Adjust the air volume
4. An medium-efficiency filter
5. An HEPA filter
6. System operation
7. HEPA filter leak detection
8. Adjust the air volume
9. Adjust the indoor static pressure difference
10. Adjust temperature and humidity
11. Determination of the average velocity and uneven velocity of the single-phase flow clean room section
12. Determination of indoor cleanliness
13. Determination of indoor plankton and sedimentation bacteria
14. Work and adjustments related to production equipment
(2) Test basis
Including specifications, drawings, design documents and technical information of equipment, etc., divided into the following two categories.
1. Design design documents, certification documents for design changes, relevant agreements, and as-built drawings.
2. The technical data of the equipment.
3. "Code for Clean Workshop Design" GB50073-20012, "Code for Construction Quality Acceptance of Ventilation and Air Conditioning Engineering" GB50243-2002
Six. Detection method and result judgment
(1) Test of air volume or wind speed
1. Sampling and testing the areas with design requirements.
2. The air volume and wind speed must first test the various effects of the purification air conditioner, and must be obtained under the designed air volume and wind speed conditions.
(1) The measured air volume value of the turbulent flow clean room system should be greater than the respective design air volume value but should not exceed 20%; the difference between the measured fresh air volume and the designed fresh air volume should not exceed ±10% of the designed fresh air volume; The difference between the air volume of each air outlet in the room and its respective design air volume should not exceed ±15% of the design air volume.
(2) The measured indoor average wind speed of the unidirectional flow laminar flow clean room should be greater than the design wind speed but should not exceed 20%; the difference between the total measured fresh air volume and the designed fresh air volume should not exceed ± 10% of the designed fresh air volume.
3. Operation process and judgment
(1) Turbulent flow clean room
a. For the tuyere without filter, it can be tested according to the air volume test method of general efficiency general ventilation and air conditioning.
b. For the tuyere equipped with a filter, the auxiliary air duct can be selected according to the form of the tuyere, that is, a straight pipe section made of a hard plate that is the same as the inner section of the tuyere and whose length is equal to twice the side length of the tuyere is connected to the filter tuyere Externally, on the outlet plane of the auxiliary air duct, the measuring points are evenly arranged according to the minimum number of measuring points not less than 6 points, and the wind speed at each point is measured with a hot-ball anemometer, and the air volume is determined by multiplying the average wind speed of the tuyere section by the net cross-sectional area of the tuyere.
c. For the tuyeres equipped with the same type of diffuser plate, according to the air volume resistance curve of the diffuser plate and the measured diffuser plate resistance, it can be found out that when the air volume is measured, use a micromanometer and a Pitot tube or use a thin rubber tube instead of a Pitot tube, but It is necessary to make the plane of the measuring hole perpendicular to the airflow direction so that the measured value can correctly reflect the static pressure value.
d. Measure the air volume with the wind hood method
① When the wind speed of each tuyere is measured by the air volume cover, the corresponding wind speed of the air outlet is Vs=As. Vs------the average air supply speed of each terminal filter or air supply diffuser m/s; Qs------the air supply volume of each terminal filter or air supply diffuser m3/s ;As------air outlet area m2.
②Unidirectional flow-laminar flow clean room The unidirectional flow clean room adopts the method of the average wind speed of the room section and the product of the cross-sectional area to determine the air supply volume, and the measurement section of the vertical unidirectional flow laminar flow clean room is 0.8m from the ground The horizontal section of the horizontal unidirectional flow laminar flow clean room is taken as a vertical section 0.5m away from the air supply surface. The distance between the measuring points on the section should not be greater than 2m, and the number of measuring points should not be less than 10. The thermal ball anemometer is used for evenly arranged instruments. .
③ Measuring the air volume in the air duct If there is a long branch pipe section on the windward side of the tuyere, and the hole has been or can be drilled, the air volume can be determined by the air duct method, and the distance between the measurement section and the local resistance component should not be less than 5 times the pipe diameter or 5 times the length of the large side.
For rectangular air ducts, divide the measurement section into several equal small sections, and each small section is as close to the side length of the square as possible, preferably no more than 200mm. The number of points should not be less than 3.
For circular air ducts, the measurement section should be divided and the number of measurement points should be determined by the equal-area circular method. Specifically, it can be carried out according to the method of measuring the air volume of the general ventilation and air conditioning duct method of comprehensive efficiency.
(2) Test of indoor static pressure difference
1. Instruments and environmental measuring instruments Inclined micromanometers, digital micromanometers, etc. Ambient temperature Normal temperature or design temperature.
2. Sampling and testing of each adjacent area with design requirements.
3. The test results of static pressure difference should meet the following requirements.
(1) The static pressure difference between adjacent clean rooms of different levels and between clean rooms and non-clean rooms should not be less than 5Pa.
(2) The static pressure difference between the clean room and the outside should be greater than 10Pa.
(3) In a unidirectional flow laminar flow clean room with a cleanliness degree higher than 100, when the door is opened, the concentration exceeding the upper limit of the indoor level should not be measured at a place 0.6m away from the entrance and exit.
4. Operation process and judgment
(1) Close all the doors, extend the rubber hose for measurement with a diameter of preferably less than 5mm from the hole on the wall into the room not far from the wall, and set it perpendicular to the airflow direction without obstructing the airflow disturbance around it.
(2) The static pressure difference should be measured from the innermost room on the plane, usually the room with the highest cleanliness level, and the pressure difference between the room next to it and the room next to it. The pressure difference between the external clean room and the surrounding auxiliary environment, and the outdoor environment.
(3) For the unidirectional flow laminar flow clean room with a cleanliness level higher than 5, the number of particles at the height of the indoor working surface at a distance of 0.6m from the door should also be measured when the door is opened.
5. Precautions during testing
Before testing the static pressure difference in the clean room, it must be verified whether the air supply volume, return air volume, and exhaust air volume are in line with the specified air volume under the condition that the doors that should be closed are all closed when the clean room or clean facility is working normally . If the requirements of the standard cannot be met, the fresh air volume and exhaust air volume should be readjusted until they are qualified.
(3) Leakage of the air filter
1. Instruments and environmental measuring instruments Dust particle counters, aerosol generators. Ambient temperature Normal temperature or design temperature.
2. Before the sampling high efficiency filter body enters the site, the manufacturer should conduct a performance test according to the regulations and provide a certificate of conformity. The high-efficiency air filters installed in the unidirectional flow clean room should be leak tested one by one. For the clean room of level 7 or lower in the turbulent flow clean room, as long as the clean room reaches the required air cleanliness level, it can be No leak detection is performed.
3. Technical requirements The results of leak detection must meet the conditions: the leakage concentration measured on the downwind side of the tested filter is converted into a transmittance. The ultra-high efficiency filter should not be greater than 3 times the factory-qualified transmission rate.
5. Operation process and judgment The leak detection of the filter means that the leak detection of the installed air filter is suitable for an empty or static clean room.
For high-efficiency filters installed at the ends of the air supply and exhaust, the scanning method should be used for the filter installation frame and full-section leak detection. The scanning methods include leak detector method, photometer method and particle counter with a minimum sampling volume of 1L/min. There are two methods.
(4) Air cleanliness level
1. Instruments and environmental measuring instruments dust particle counter. Ambient temperature The temperature and relative humidity of the clean room area should be compatible with its production and process requirements.
2. The location and quantity of sampling points a. The minimum sampling amount for each determination of cleanliness; b. The minimum number of sampling times for each clean area is 3 times. When there is only one sampling point in the clean area, the Sampling at least 3 times; d. The sequential sampling method stipulated in Appendix F of ISO14644-1 can be used for a large amount of environmental sampling where the expected air cleanliness level reaches level 4 or cleaner.
3. Technical requirements ① The average particle concentration Ci of each sampling point should be less than or equal to the limit value specified in the cleanliness level; ② The 95% upper confidence limit of the average particle concentration N of all sampling points should be less than or equal to the cleanliness Class-specified limits.
4. Operation process and judgment ① After the instrument is turned on and warmed up to be stable, the instrument can be calibrated in accordance with the provisions of the instruction manual, self-inspection, self-calibration, and zero counting; Continuous reading can only be started after confirming that the count is stable; ③The sampling port of the counter and the working position of the instrument should be at the same air pressure and temperature to avoid measurement errors; ④For unidirectional flow clean room, the sampling port should face the direction of air flow; The upward sampling speed of the sampling port should be as close as possible to the indoor airflow speed; ⑤ record data evaluation.
5. Problems that should be paid attention to in the detection and sampling of suspended particles in the air in the clean room ① During the static test, there should be no more than 2 testers in the room The non-unidirectional flow should start after the normal operation time of the purified air conditioning system is not less than 10 minutes, and the non-unidirectional flow should not be less than 30 minutes; ③ The instrument must be calibrated regularly according to the instrument’s calibration cycle. It depends on the characteristics of the instrument itself, the frequency of use, and the use environment; ④Each sampling point can sample air according to the calculated minimum sampling volume. However, generally according to the sampling volume and time setting of the particle counter used, the actual sampling volume may be higher than the minimum sampling volume. ⑤ When measuring, the personnel entering the clean room should wear clean clothes, and the air shower should pass through the air shower, and try to be in the downwind of the room and stay still and move less.
6. Indoor planktonic bacteria and sedimentary bacteria There are many kinds of determination of suspended microorganisms in the air, but the basic process of the determination is the process of capture, culture and counting. At present, the test of planktonic bacteria and sedimentary bacteria is used method.
(1) Instruments and environmental measuring instruments Petri dishes, centrifugal microbial samplers, constant temperature incubators, planktonic bacteria, sedimentation bacteria before testing, the temperature and humidity of the tested clean room area must meet the specified requirements, static pressure difference It must be controlled within the specified value, and the tested clean room area has been disinfected.
The preparation of the sampling device before sampling and the treatment after sampling should be carried out in the negative pressure laboratory where the high-efficiency filter is exhausted. There are two test states: static and dynamic, and the test state should be indicated in the report. Testers Testers must wear work clothes that meet the cleanliness level of the environment. During the static test, indoor testers should not exceed 2 people.
(2) The position and quantity of sampling points The indoor planktonic bacteria measuring point and the cleanliness measuring point can be the same, and the sampling must be carried out according to the steps specified in the instrument manual, and special attention should be paid to the disinfection and sterilization of the instrument before testing. During the determination of sedimentation bacteria, the petri dishes should be arranged in representative places and places with minimal airflow disturbance.
(3) Technical requirements Indoor plankton and sedimentation bacteria should meet the design requirements.
(4) Operation process and judgment
①Test of planktonic bacteria a. Strict disinfection should be carried out on the surface of test instruments and petri dishes first. Samplers used in Class 5 clean rooms should always be placed in the clean room. b. Samplers should wear clean clothes and disinfect their hands. c. Start the vacuum pump to pump air so that the residual disinfectant in the instrument evaporates for no less than 5 minutes, and adjust the speed of the flow dial. Turn off the vacuum pump and place the Petri dish with the lid on to adjust the sampler. d. After setting the sampling port at the sampling point, turn on the sampler, vacuum pump, and rotation timer in turn, and select the sampling time according to the sampling volume. After all the samples are collected, place the petri dish upside down in a constant temperature incubator at 30-35°C, and cultivate for no less than 48 hours. e. Count directly with the naked eye, and then use a 5-10 times magnifying glass to check whether there is any omission. If there are two or more colonies on the plate for overlapping resolution, count as two or more colonies.
②The test of sedimentation bacteria should start after no less than 10 minutes of normal operation of the purification air conditioning system for unidirectional flow such as class 5 purification room and laminar flow workbench; for non-unidirectional flow such as class 7 and 8 The above purification room test should start after the normal operation of the purification air conditioning system for no less than 30 minutes.
a. Sampling method: place the prepared petri dish at a predetermined sampling point, open the lid of the petri dish to expose the surface of the culture medium for 0.5 hours, then cover the petri dish and invert it. b. After all the sampling of the culture is completed, the petri dish is placed upside down in a constant temperature incubator for culture. Incubate at 30-35°C for no less than 48 hours. Each batch of culture medium should have a control test to check whether the culture medium itself is contaminated, and 3 petri dishes can be selected for each batch for control culture. c. Count the colonies directly with the naked eye and then use a 5-10 times magnifying glass to check for omissions. If 2 or more colonies overlap and can be distinguished on the petri dish, count as 2 or more colonies.
5. Precautions ① The test equipment should be sterilized to ensure the reliability and correctness of the test. ② Take all measures to prevent artificial contamination of samples. ③ Make detailed records of culture medium, culture conditions and other parameters. ④Because there are many kinds of bacteria with great differences, when counting, generally use transmitted light on the back or front of the petri dish, carefully observe the colonies growing on the edge of the petri dish, and pay attention to the difference between bacterial colonies and culture medium sediments, if necessary, use Microscopic identification. ⑤The quality of each petri dish should be carefully checked before sampling. If any deterioration, damage or contamination is found, it should be discarded.
(5) Indoor air temperature and relative humidity
1. Instruments and environment Commonly used instruments and equipment include wet and dry bulb thermometers, digital hygrometers, mercury thermometers, etc.
2. Layout and quantity of measuring points See the table above for the number of measuring points.
3. Technical requirements
(1) For places without constant temperature requirements, the temperature and humidity indicators should meet the design requirements.
(2) For places with constant temperature and humidity requirements, the room temperature fluctuation range is organized into a cumulative statistical curve according to the percentage of the maximum value of the temperature deviation from the control point in each temperature of each measuring point to the total number of measuring points. More than 90% of the measuring points reach The deviation value of the room temperature fluctuation range should meet the design requirements. Relative humidity fluctuation range can be determined according to the principle of room temperature fluctuation range.
4. Operation process and judgment
(1) Determine the working area according to the design requirements and cleanliness level, and arrange the measuring points in the working area. The cleanliness room is 0.5m away from the enclosure structure, and the working area is 0.5-1.5m away from the ground.
(2) According to the temperature and humidity fluctuation range, the clean room should be continuously required for 48 hours, and the interval between each reading should not be greater than 30 minutes.
(3) For rooms without constant temperature requirements, a point in the center of the room can be measured.
(6) The average velocity and uneven velocity of the cross-section of the single-phase flow clean room
1. Instruments and environmental instruments and equipment thermal bulb anemometer. Ambient temperature Normal temperature or design temperature.
2. Sampling should be tested for the average wind speed of the cross-section of the unidirectional flow clean room.
The cross-sectional wind speed unevenness of the unidirectional flow clean room with a cleanliness level higher than 5 is required to be tested, and the unidirectional flow clean room with a cleanliness level of 5 is tested when the design requires it.
3. Technical conditions (1) The measured indoor average wind speed should be greater than the design wind speed but not more than 20%. (2) The wind speed non-uniformity calculated by the following formula should not be greater than 0.25v1β.
4. Operation process and judgment (1) The measurement section, the number of measurement points and the measurement instruments should meet the requirements of the unidirectional flow laminar flow clean room
More news
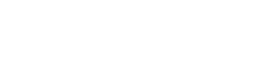
9/F, Building 5, Area A, Hongchuang Science and Technology Center, Longhua District, Shenzhen
© Copyright Shenzhen King Medical Testing Technology Co., Ltd. All rights reserved.